A Voltage Transformer Factory is a manufacturing facility that produces and supplies electrical transformers. The facility offers a wide range of products that include power, isolation, current, step-up, and step-down transformers. It also provides marking, labeling, packaging, and documentation services. The company has been in business since 1971 and is based in Fort Worth, TX.
Voltage transformers are passive machines that transfer electrical energy from one circuit to another through the application of magnetic flux. They are used in a variety of industries such as electronics, telecommunications, and transportation.
In a transformer, the magnetic flux travels through the core and then through the windings. The core is typically made of a thin steel layer. It is insulated to reduce eddy current losses and hysteresis losses. The core is surrounded by the primary and secondary windings.
The windings are the parts of a transformer that contain the magnetic flux and carry the electric current. They are constructed by stacking and laminating thin iron or steel sheets to provide a low reluctance path for the magnetic flux. The sheets are insulated from each other to avoid carbon buildup, and the windings are mounted on the core using nuts and bolts.
Some transformers have a solid insulating material, such as paper or pressboard. However, these materials are not durable and must be replaced frequently due to their degrading properties. In order to enhance insulation and improve service life, transformer oils are often used instead. These oils consist of hydrocarbon mineral oils such as aromatics, paraffin, and naphthene.
Tests and Inspection
There are a number of tests that can be done on a transformer to determine its safety and reliability. These include applied-voltage and induced-voltage tests. The former uses a high voltage to test the turn-to-turn insulation and the latter uses a higher excitation voltage to test the quality of the core saturation protection.
During an applied-voltage test, a high voltage is inserted through the entire winding of the transformer, and each winding is tested for its turn-to-turn insulating capability. The voltage is increased gradually over 15 seconds and then held there for 40 seconds before being reduced back to zero.
If the transformer passes this test, it can be safely operated without a risk of arcing or overloading. The test results can also be used for fault detection and troubleshooting purposes.
The test is usually performed in a laboratory with an electrical conductivity meter. The primary and secondary voltages of the transformer are measured using a voltmeter, and the load loss and impedance voltage are calculated using an ammeter and wattmeter.
The resulting voltages are then compared to a known reference value. If the difference is less than 5%, the transformer is deemed safe and can be installed in the field. If the difference is more than 5%, it can be a sign that the transformer needs to be replaced. This can be a costly replacement, as it may require new windings and cores.
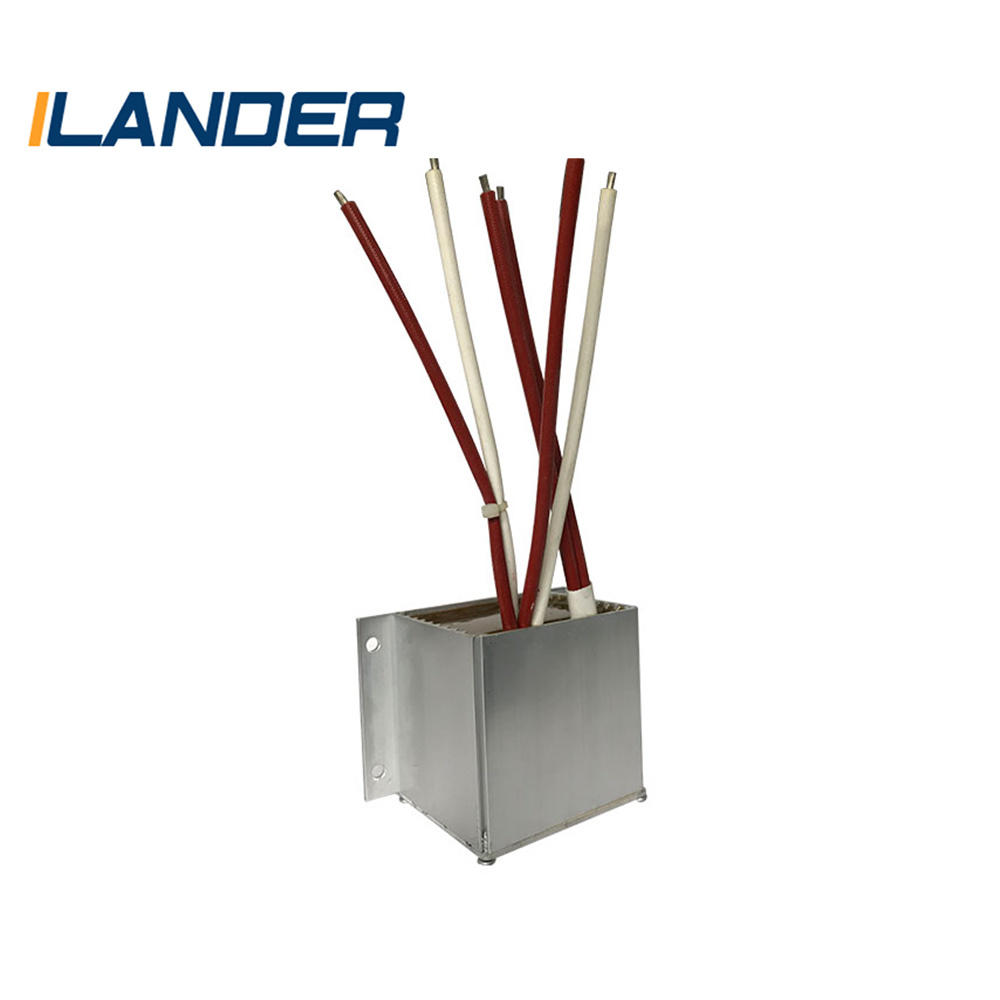