Intermediate frequency furnaces require special transformers known as rectifier transformers due to their unique requirements. Unlike ordinary transformers, rectifier transformers have higher impedance and smaller harmonics. While transformers such as S9 and S11 are commonly used in civilian applications, they are not suitable for intermediate frequency furnaces due to differences in voltage and impedance requirements.
Intermediate frequency furnaces typically operate on industrial electricity, which is usually supplied at 380V. In contrast, ordinary transformers used in civilian applications operate at 220V. Although the principles and structures of these transformers are similar, the impedance requirements for intermediate frequency furnace transformers are different. Additionally, the high and low voltage coils of intermediate frequency furnace transformers require grounding and shielding to ensure safety and proper operation.
Manufacturing special transformers for intermediate frequency furnaces requires careful calculation of parameters and selection of high-quality materials. High-permeability and low-loss silicon steel sheets are used to make the core and wire of the transformer. The copper to iron ratio is determined using scientific methods to minimize no-load loss and noise. Furthermore, effective heat and current control measures, such as the "open source and throttling" method, are implemented during manufacturing to ensure stable and efficient transformer operation.
Transformers for intermediate frequency furnaces are specialized rectifier transformers designed to meet the unique requirements of industrial applications. Through precise calculation of parameters, selection of high-quality materials, and implementation of effective control measures, these transformers ensure reliable and efficient operation of intermediate frequency furnaces in various industrial settings.
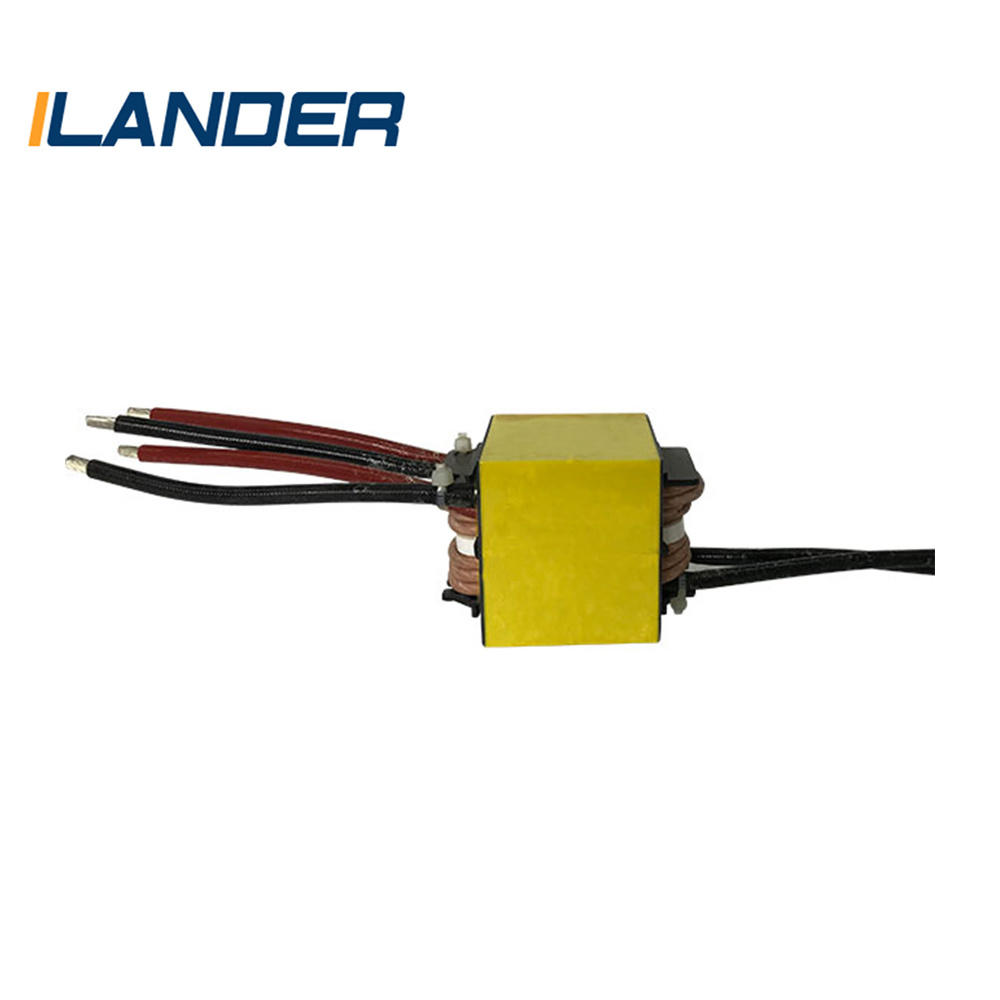
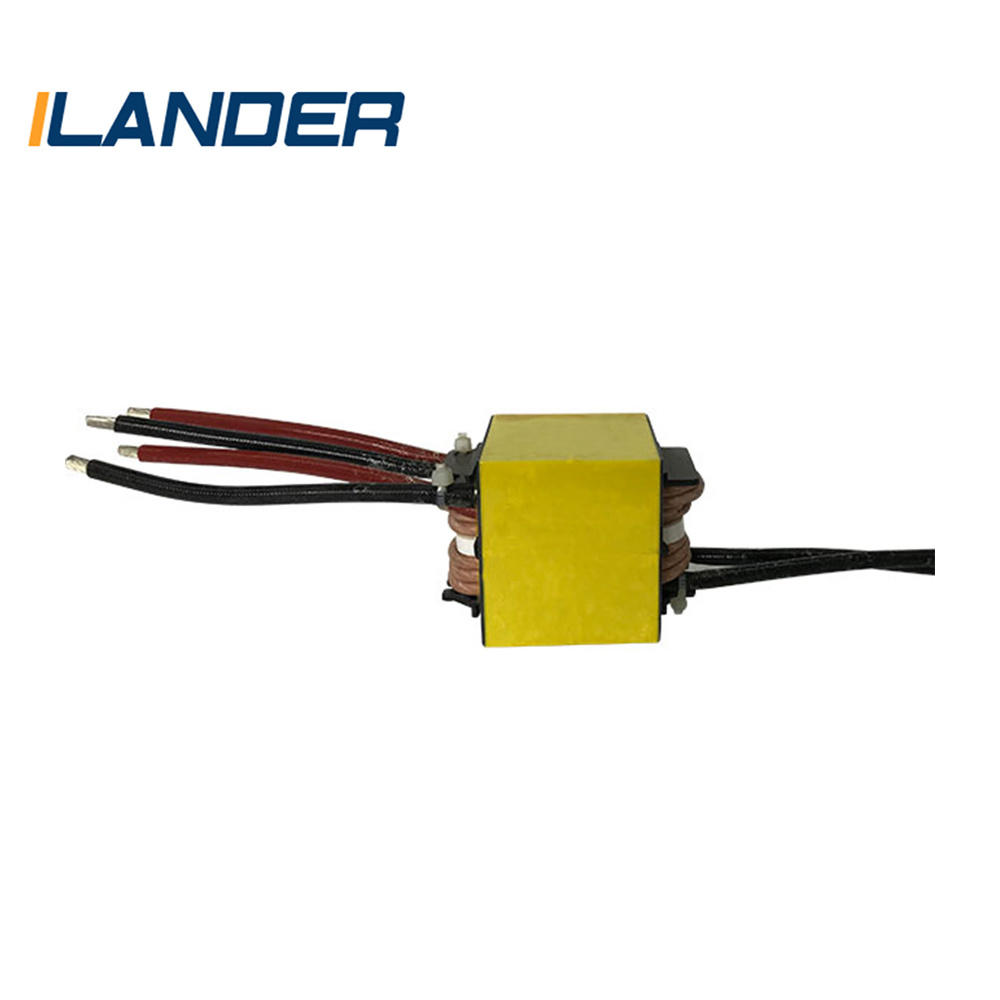