Enameled wire greatly improves the insulation strength, so most low-power transformers below 50W adopt the flame-retardant plastic skeleton stack winding method. However, high-strength enameled wire must be used, and the wires should still be arranged in turns during winding. Large diagonal spans are strictly prohibited. To avoid increasing the potential difference between wires.
For transformers above 50W, due to the reduced number of turns per volt and the high voltage difference between wires, it is best to pad each layer with insulating paper (0.05mm thick cable paper. Kraft paper). The upper wires should be absolutely avoided during winding. Slide into lower level. The insulation between each winding should be determined according to the winding voltage.
More than 4 layers of 0.1mm cable paper should be placed between the primary and secondary ends. Avoid using self-adhesive tape. If the secondary winding of the small-power transformer using the above-mentioned stack winding method has more than two sets of windings, two layers of cable paper insulation should be used between each set. If the transformer is used in audio or audio-visual equipment, an electrostatic shielding layer should be inserted between the primary and secondary in the multi-layer winding method.
More than 4 layers of 0.1mm cable paper should be placed between the primary and secondary ends. Avoid using self-adhesive tape. If the secondary winding of the small-power transformer using the above-mentioned stack winding method has more than two sets of windings, two layers of cable paper insulation should be used between each set. If the transformer is used in audio or audio-visual equipment, an electrostatic shielding layer should be inserted between the primary and secondary in the multi-layer winding method.
After winding, attention should also be paid to inserting the silicon steel sheet and it must be inserted tightly to avoid electromagnetic noise. Regardless of the double E shape or EI shape, the ports must be in close contact. They should be cross-inserted without any gaps. The last 4 to 5 pieces can be inserted from the middle to avoid damaging the wire package.
Then dry and dip in paint. For transformers below 50W, the internal heat method can be used for drying. The method is: short-circuit all the secondary windings of the transformer and connect it to the mains in series with a 60~100W/220V light bulb to make it heat up automatically. The larger the bulb, the higher the temperature, but in a sealed state, it is safer to keep the temperature below 80 degrees.
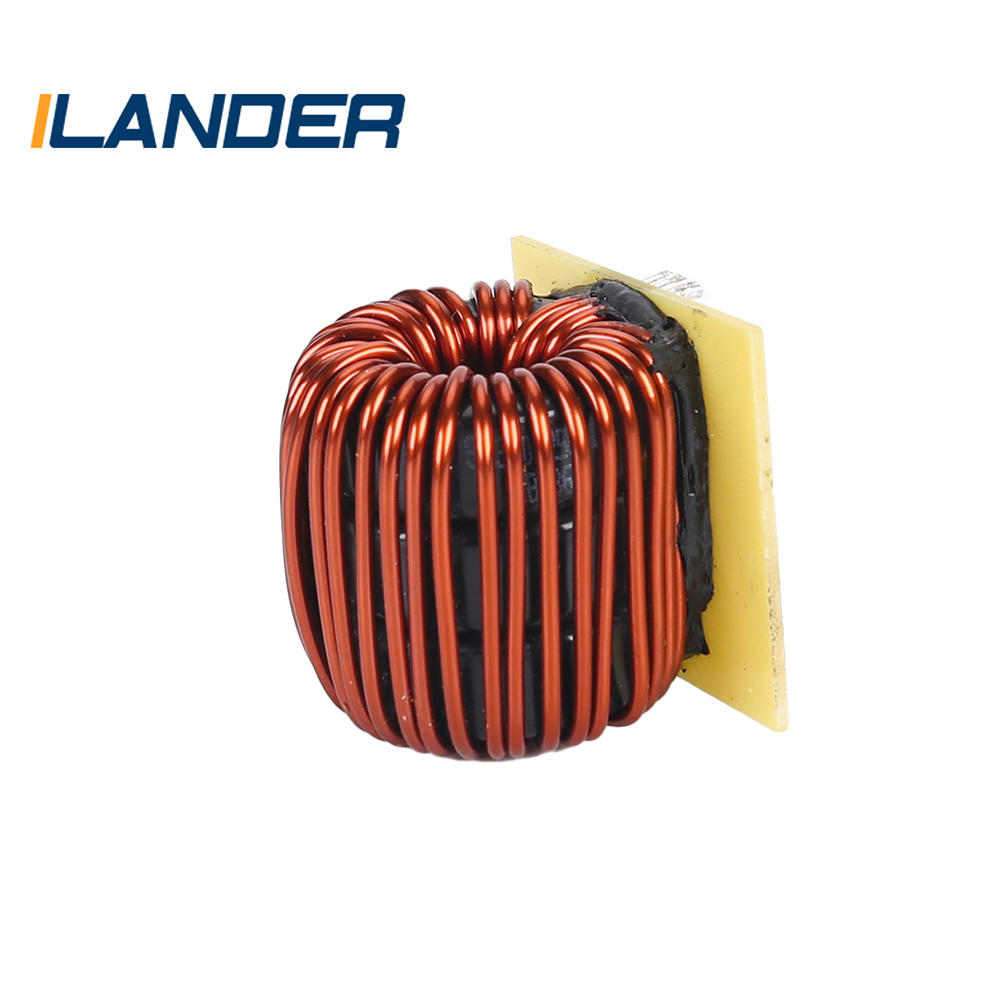
Then dry and dip in paint. For transformers below 50W, the internal heat method can be used for drying. The method is: short-circuit all the secondary windings of the transformer and connect it to the mains in series with a 60~100W/220V light bulb to make it heat up automatically. The larger the bulb, the higher the temperature, but in a sealed state, it is safer to keep the temperature below 80 degrees.
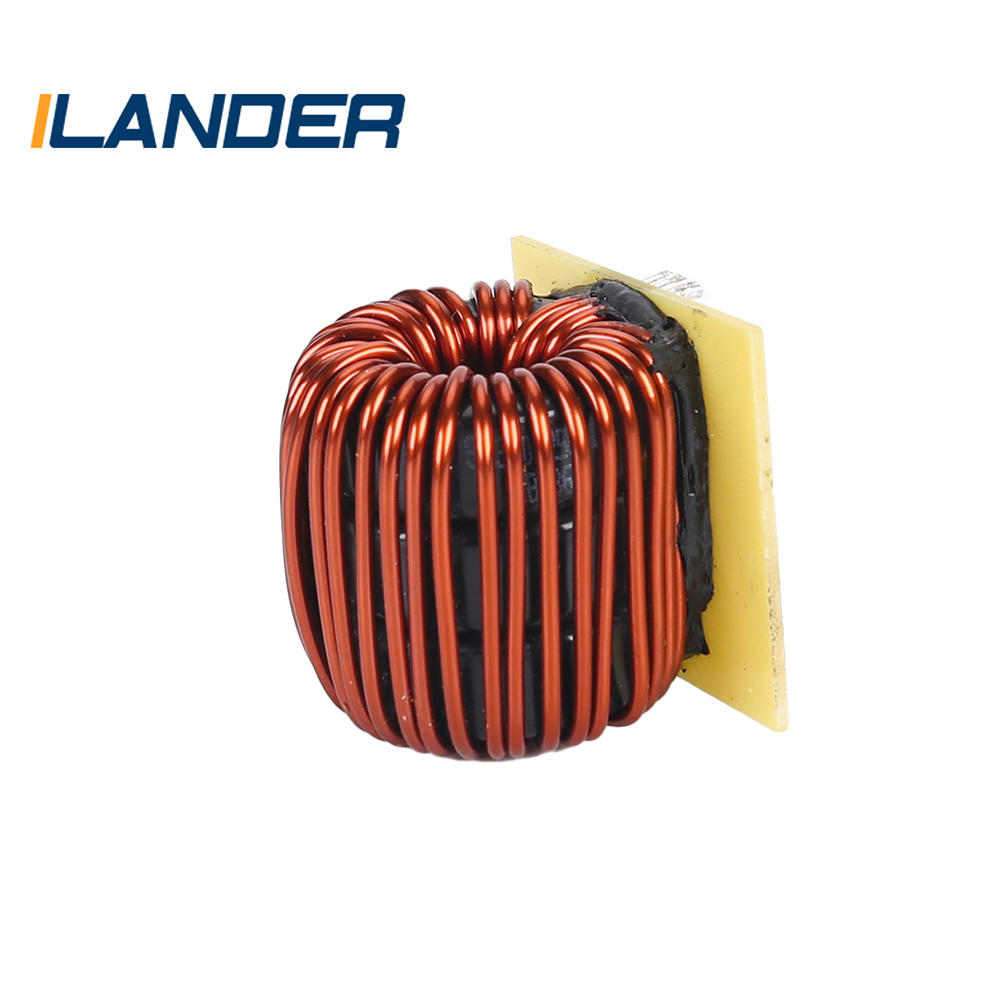