In 2023, the transformer industry experienced significant growth and development, marking one of the best periods in the last 50 years. This surge in demand can be attributed to several factors, including the increasing adoption of renewable energy sources and the need for replacing aging infrastructure in mature markets. As a result, all leading transformer manufacturers found themselves fully booked, with delivery timelines extending by 12-18 months.
The rise in demand for transformers can be directly linked to the shift towards renewable energy. For instance, while a traditional 500 MW thermal power plant may require only 4-6 transformers when added to the grid, a solar farm of the same capacity may necessitate anywhere between 70 to 200 transformers. Despite the total transformer MVA (mega-volt-ampere) being similar for both thermal and solar power stations, the utilization factor of solar power requires a much higher number of transformers to generate an equivalent amount of energy. This discrepancy underscores the need for the transformer industry to focus on developing reliable, low-loss, and maintenance-free transformers tailored for the renewable energy sector.
Furthermore, the increasing demand for green hydrogen and electric vehicles is expected to further drive the demand for transformers in the coming years.
While the structure of power transformers remains largely similar across different voltage levels, the installation procedures may vary due to transportation and insulation requirements. Power transformers with voltages of 220KV and above are typically transported with nitrogen, and the installation process may involve specific protocols for handling transformers transported with oil.
During transformer handling, it is crucial to protect the porcelain insulation. Using cloth boxes or cartons to cover the upper and lower pressure porcelain insulation can prevent damage. Additionally, care should be taken to avoid impact or excessive vibration during transportation, and mechanical traction should be used with the traction point positioned below the transformer's center of gravity to prevent tilting. The tilt angle during transportation should not exceed 15 degrees to prevent structural deformation.
Before handling or loading/unloading large transformers, it is essential to check the direction of the upper and lower pressure sides to avoid difficulties during installation. By adhering to these guidelines, the transformer industry can ensure the safe and efficient transportation and installation of transformers to meet the growing demand in the evolving energy landscape of 2023 and beyond.
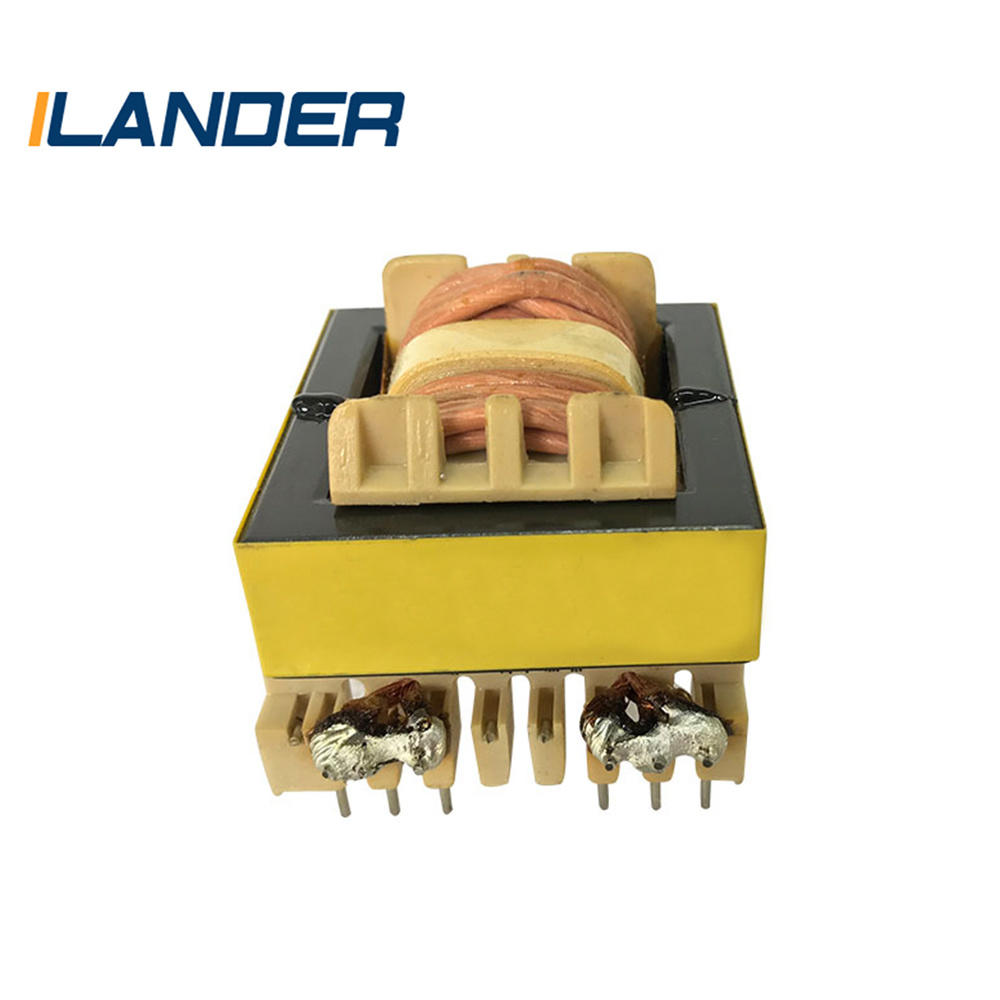
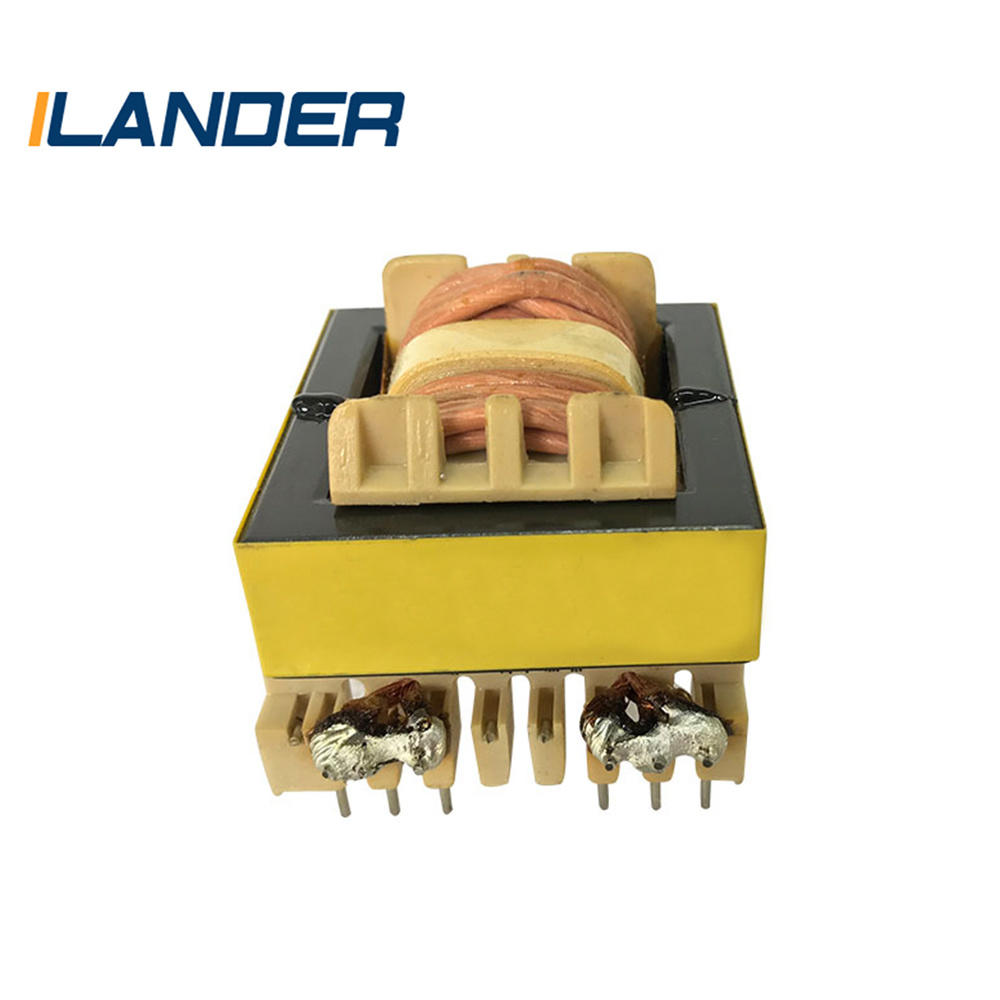