The winding method employed in an R-type transformer is a critical aspect of its design, directly influencing the turns ratio between the primary and secondary windings and consequently determining the output voltage. Different winding methods are available, each offering unique advantages and considerations based on design requirements. Three common winding methods for R-type transformers include single-layer winding, split winding, and alternating winding.
Single-Layer Winding:
Method: In single-layer winding, both the main and auxiliary windings are wound using only one layer of wire. The windings are arranged perpendicularly to each other on the transformer core.
Advantages: Single-layer winding is the simplest method, requiring less complex manufacturing processes. It is often chosen for applications where simplicity is prioritized, and space constraints permit a single layer of winding.
Considerations: This method may result in a larger physical size for the transformer due to the single-layer configuration.
Split Winding:
Method: In split winding, the main winding and the secondary winding are wound on different cores, ensuring that their magnetic circuits do not interfere with each other. This separation can help mitigate unwanted interactions between the windings.
Advantages: Split winding provides improved isolation between the main and auxiliary windings, reducing the risk of magnetic interference and enhancing overall transformer performance.
Considerations: This method may involve more complex manufacturing processes compared to single-layer winding.
Alternating Winding:
Method: Alternating winding involves using two different specifications of wire to wind the main and auxiliary windings separately, achieving a specific ratio of turns.
Advantages: This method allows for fine-tuning of the turns ratio and can provide greater flexibility in meeting specific design requirements.
Considerations: Alternating winding requires careful attention to wire specifications and precise winding techniques to achieve the desired turns ratio accurately.
The selection of the winding method depends on the specific design goals, application requirements, and trade-offs between simplicity, space constraints, and desired performance characteristics. Engineers and designers carefully evaluate these factors to choose the most suitable winding method for a given R-type transformer application, ensuring optimal efficiency and functionality.
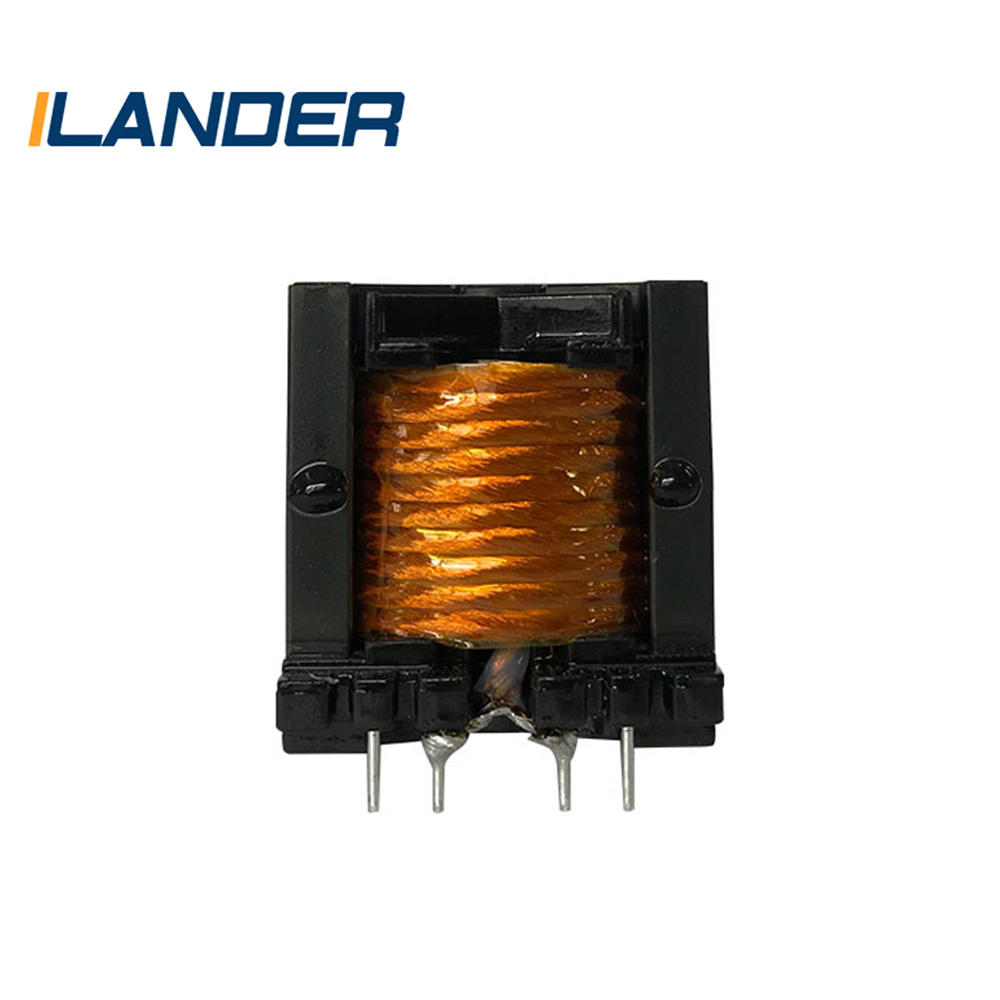
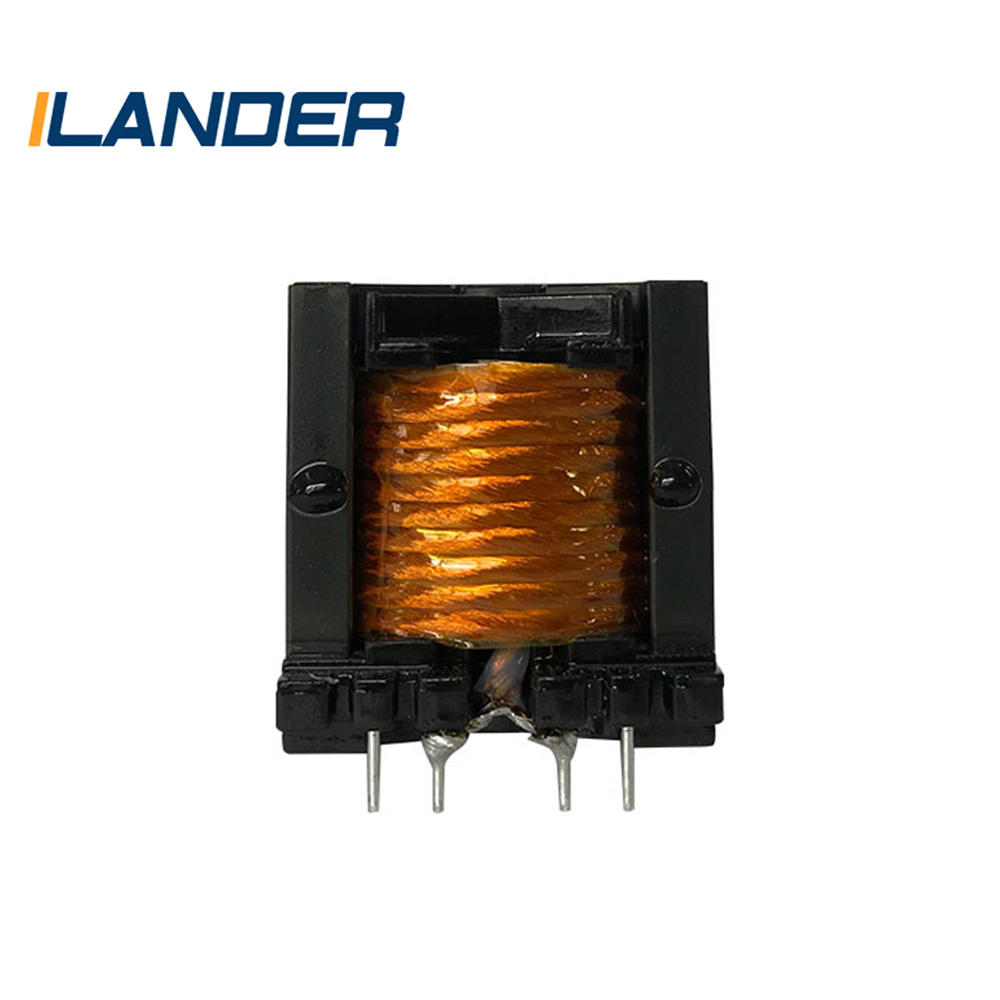