1. Immersed dry-type transformer
This kind of transformer has the longest production history, and the manufacturing process is relatively simple. The wire is covered with glass fiber, and the spacer is hot-pressed with the corresponding insulation grade material. Depending on the impregnating varnish, the insulation grade of the transformer is divided into B, F, H, and C grades, and the empty channels of the main longitudinal insulation are all made of air as the insulating material. Because this kind of transformer is more affected by the external environment than resin, the output tends to decrease both at home and abroad.
2. Resin dry-type transformer
Resin dry-type transformers are divided into four structures: resin plus filler casting, resin casting, resin wrapping, and resin vacuum pressure impregnation. Although the investment in the equipment used is large, the installation and maintenance costs are low.
2.1. Resin casting and resin plus filler casting structure
The two structures are basically the same, the low-voltage winding is made of foil plate (copper or aluminum) or wire (impregnated with paint and end-sealed), and the high-voltage winding is wound with foil strip (copper or aluminum) on the epoxy glass cylinder and segmented. (8 to 12 segments), or wound into segmented cylinders with flat or round wires, and then loaded into the casting mold.
2.2. Resin wrapped structure
The low-voltage winding structure is the same as the previous structure. The high-voltage winding is carried out on the winding machine, and the inner mold is an epoxy glass fiber cloth drum. The advantage of this structure is that no casting mold is required. It takes 8 hours to wind a high-voltage winding with this structure, which is roughly the same as the time required to wind a segmented cylindrical structure of a cast high-voltage winding, and only 2 hours to wind a high-voltage foil winding. At present, the cost of this type of product in China is about 1.25 times that of resin plus filler products.
2.3. Resin vacuum pressure impregnated structure
The low-voltage winding structure is the same as the above structure. After the high-voltage winding is wound on the winding machine and pre-pressed and pre-dried, it is placed in a pouring tank for vacuum treatment. The resin is injected under vacuum to penetrate into the conductor, the entire winding is wrapped with resin, then the vacuum is released and pressure is applied to make the resin penetrate into the winding well, and then the winding is sent to the furnace for processing. Its advantage is that there is no need for casting molds, and the winding is the same as the previous ones, but vacuum pressure impregnation is required. This is a new technology developed in recent years developed products.
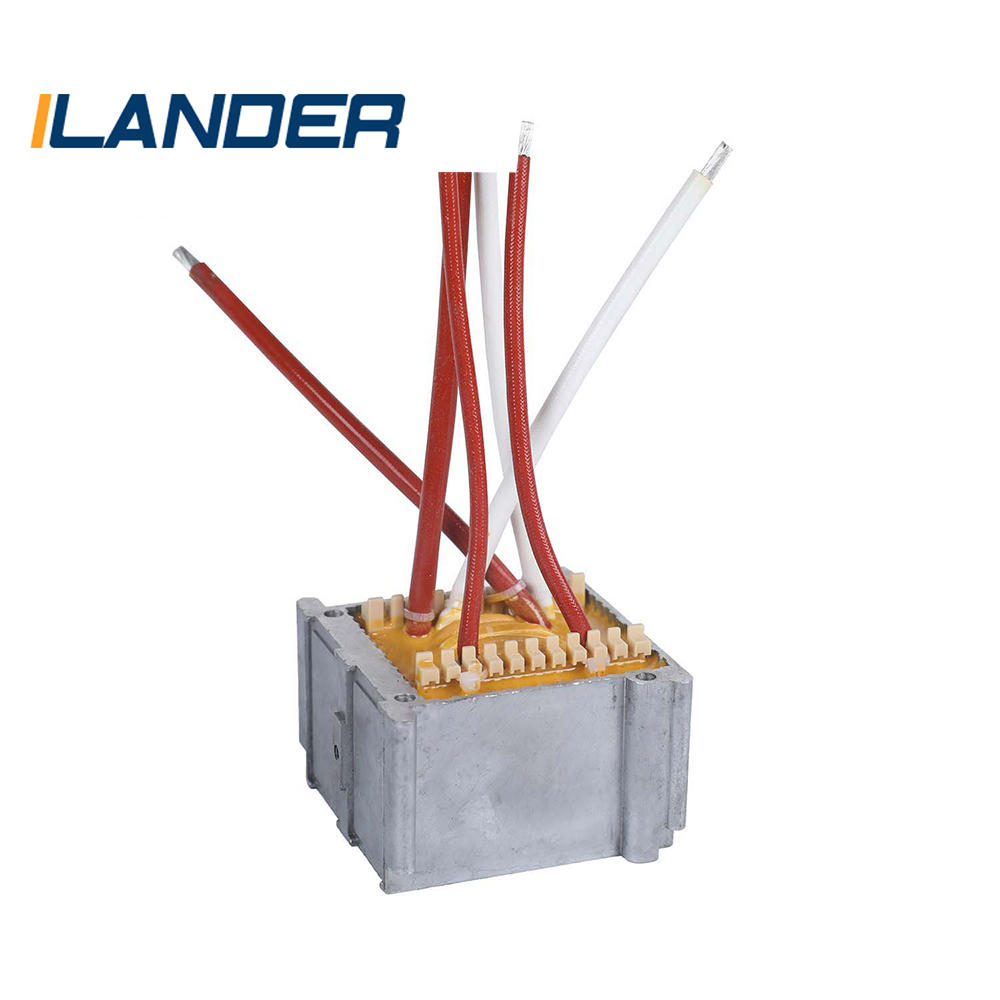